Advanced Pipeline Welding Inspection: Methods for Discovering Defects
Advanced Pipeline Welding Inspection: Methods for Discovering Defects
Blog Article

Best Practices for Pipeline Welding Evaluation: Techniques, Standards, and Treatments to Attain Quality Assurance and Conformity
Reliable pipe welding inspection is essential for guaranteeing the integrity and safety of crucial infrastructure. Understanding the complexities included in each stage of assessment is vital to accomplishing compliance and reliability in pipeline systems.
Importance of Welding Examination
The honesty of bonded joints is critical in ensuring the security and dependability of pipeline systems. Correct welding techniques and thorough examination procedures are essential to protect against failings that can result in catastrophic cases, ecological damages, and loss of life. Pipeline Welding Inspection. Welding examination offers as a safety net, recognizing flaws such as cracks, porosity, and incomplete combination prior to they escalate right into major concerns
Additionally, pipe systems typically run under high pressure and severe conditions, making the top quality of welds a lot more crucial. Regulative compliance is an additional significant facet, as numerous requirements dictate the high quality assurance procedures that should be stuck to in pipe construction and upkeep. Failure to conform can cause monetary losses and legal ramifications.

The function of welding examination extends past plain verification of handiwork; it includes the guarantee of lasting operational integrity. This includes an organized technique that consists of not only visual evaluations however additionally progressed non-destructive testing approaches. Ultimately, effective welding assessment is a financial investment in the long life and safety and security of pipeline systems, guaranteeing they work as intended while minimizing risks related to product shortages.
Secret Evaluation Methods
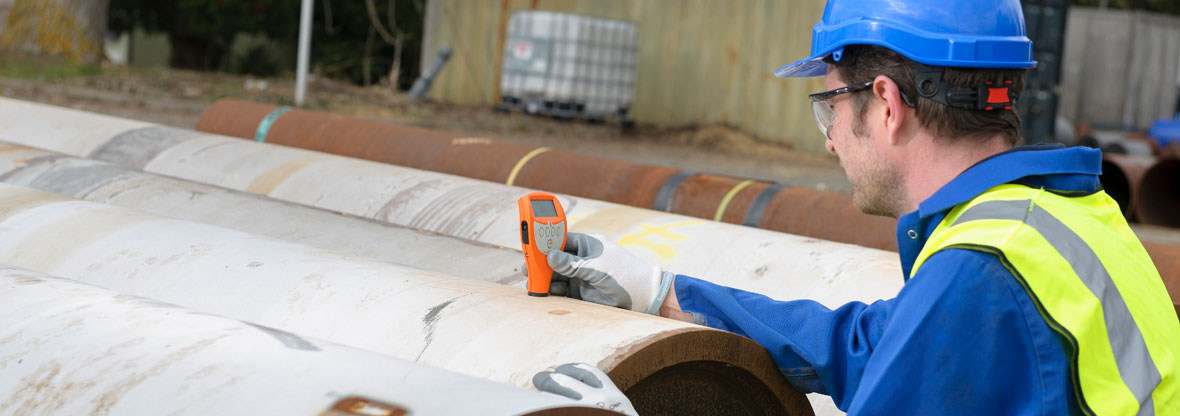
Visual inspection, usually the first line of protection, permits the identification of surface flaws such as splits, undercuts, and porosity. Ultrasonic screening employs high-frequency sound waves to find internal problems, providing a comprehensive analysis of weld stability. This non-destructive method is particularly effective for determining suspensions that may not show up on the surface.
Radiographic testing entails making use of X-rays or gamma rays to produce pictures of the welded joint, exposing inner issues. This strategy gives detailed understandings yet might call for customized devices and security factors to consider. Last but not least, magnetic fragment screening works for discovering surface and near-surface discontinuities in ferromagnetic materials, making use of magnetic fields and great iron particles.
Industry Criteria and Laws
Conformity with market standards and regulations is essential for making certain the high quality and safety and security of pipeline welding inspections. These requirements provide a structure for ideal practices in welding procedures, products, and evaluation techniques, allowing companies to decrease flaws and enhance the honesty of pipeline systems. Trick bodies such as the American Society of Mechanical Designers (ASME), the American Welding Culture (AWS), and the International Organization for Standardization (ISO) set forth standards that are commonly identified and embraced within the market.
In the United States, laws from the Pipeline and Hazardous Products Security Administration (PHMSA) regulate the safety of pipe operations, mandating rigorous evaluation protocols. These standards not just serve to shield public security and the setting however also guarantee conformity with legal and legal commitments. Adherence to the relevant codes, such as ASME B31.3 for procedure piping, is necessary for maintaining functional performance and regulative conformity.
Furthermore, constant updates and alterations to these standards mirror technological improvements and advancing industry methods, stressing the need for organizations to remain informed and train workers appropriately. Inevitably, robust compliance with well established criteria fosters depend on and integrity in pipeline infrastructure, protecting both properties and stakeholders.
Effective Inspection Procedures
Efficient examination treatments are essential for determining prospective flaws in pipe welds and ensuring the overall stability of the system. A methodical technique to assessment incorporates a number of crucial stages, consisting of pre-weld, in-process, and post-weld examinations. Each stage plays an essential duty in keeping quality control.
Throughout pre-weld examination, it is vital to evaluate the products and joint arrangements, making certain conformity with task specs. In-process assessments include monitoring welding techniques and criteria, such as warmth input and take a trip speed, to prevent defects from taking place. This phase enables real-time modifications to welding methods.
Post-weld inspections consist of non-destructive screening (NDT) methods like radiography, ultrasonic testing, and magnetic fragment testing. These methods aid find interior and surface imperfections that might jeopardize the pipe's capability. Paperwork of all examination activities is paramount, giving a traceable record that sustains compliance with sector criteria.
Training and certification of examination personnel further improve the efficiency of these procedures. By adhering to an organized evaluation method, organizations can mitigate dangers, guarantee conformity, and inevitably provide pipelines that fulfill rigid security and efficiency requirements.
Usual Challenges and Solutions
Pipe welding evaluation provides several typical obstacles that can affect the quality and security of the last item. One substantial difficulty is the irregularity in welding techniques and materials, which can bring about irregular weld high quality. To resolve this, it is important to establish standard treatments and training for welders, guaranteeing a consistent approach across jobs.
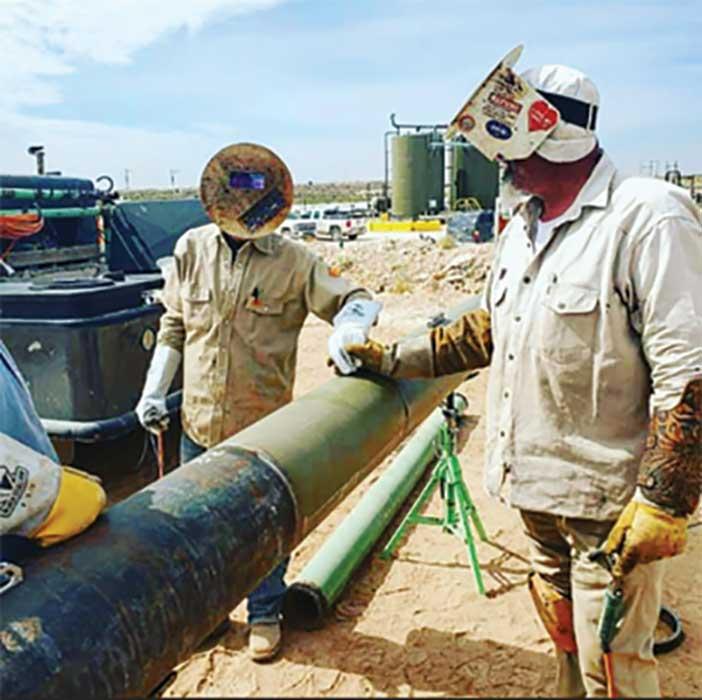
Environmental variables, including temperature level and humidity, can also affect the welding procedure, potentially causing splits or insufficient blend. Carrying out regulated environments and sticking to pre-weld procedures can alleviate these threats.
Final Thought
Finally, the application of ideal practices for pipe welding inspection is essential for guaranteeing quality guarantee and conformity with sector standards. A detailed method, incorporating various techniques such as visual, ultrasonic, and radiographic testing, facilitates the identification of problems throughout all phases of the welding procedure. Pipeline Welding Inspection. Adherence to developed policies and reliable assessment treatments not only improves the integrity and security of pipe systems but likewise mitigates dangers linked with welding defects, thus promoting general functional honesty
Compliance with industry requirements and guidelines is essential for ensuring the high navigate to this site quality and safety and security of pipe welding inspections. These standards offer a structure for finest techniques click here now in welding procedures, products, and examination techniques, allowing organizations to reduce flaws and improve the stability of pipe systems.In the United States, guidelines from the Pipe and Hazardous Products Security Management (PHMSA) regulate the security of pipeline operations, mandating rigorous evaluation protocols. A methodical method to evaluation includes several key phases, including pre-weld, in-process, and post-weld examinations.In final thought, the application of best practices for pipe welding inspection is important for ensuring quality guarantee and compliance with industry standards.
Report this page